Professional Records
License Records
Brian P Resnick
License #:
CPA00692 - Active
Category:
Physician Assistant
Issued Date:
Jun 2, 2013
Expiration Date:
Jun 30, 2017
Type:
CSR-Physician Assistant
Brian M Resnick
License #:
OT003972T - Expired
Category:
Osteopathic Medicine
Type:
Graduate Osteopathic Trainee
Medicine Doctors
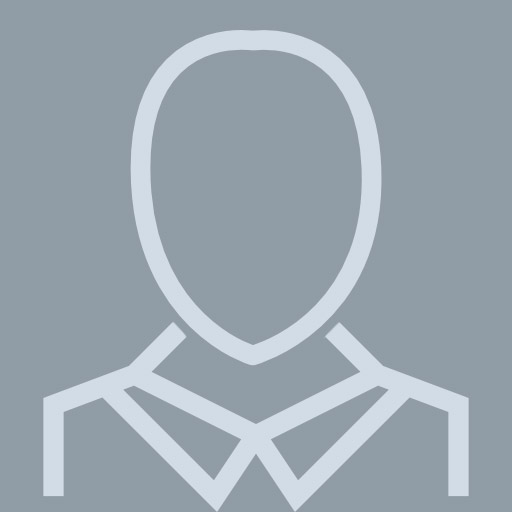
Brian M. Resnick
View pageSpecialties:
Internal Medicine
Work:
County Line Medical Associates
706 S County Line Rd, Telford, PA 18969
(215) 723-7300 (phone), (215) 723-8022 (fax)
706 S County Line Rd, Telford, PA 18969
(215) 723-7300 (phone), (215) 723-8022 (fax)
Education:
Medical School
Philadelphia College of Osteopathic Medicine
Graduated: 1993
Philadelphia College of Osteopathic Medicine
Graduated: 1993
Procedures:
Allergen Immunotherapy
Arthrocentesis
Destruction of Benign/Premalignant Skin Lesions
Electrocardiogram (EKG or ECG)
Skin Tags Removal
Vaccine Administration
Arthrocentesis
Destruction of Benign/Premalignant Skin Lesions
Electrocardiogram (EKG or ECG)
Skin Tags Removal
Vaccine Administration
Conditions:
Acne
Acute Bronchitis
Acute Pharyngitis
Acute Sinusitis
Acute Upper Respiratory Tract Infections
Acute Bronchitis
Acute Pharyngitis
Acute Sinusitis
Acute Upper Respiratory Tract Infections
Languages:
Chinese
English
Spanish
Vietnamese
English
Spanish
Vietnamese
Description:
Dr. Resnick graduated from the Philadelphia College of Osteopathic Medicine in 1993. He works in Telford, PA and specializes in Internal Medicine. Dr. Resnick is affiliated with Abington Memorial Hospital, Grand View Hospital and St Lukes Hospital Allentown Campus.