Resumes
Resumes
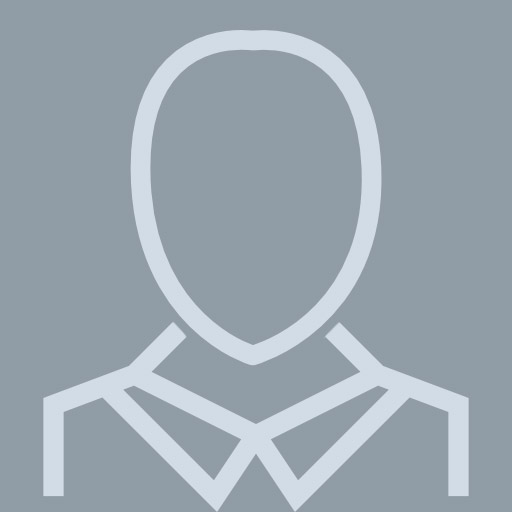
Guangyu Li
View pageLocation:
Portland, OR
Skills:
Laser
Optics
Optics
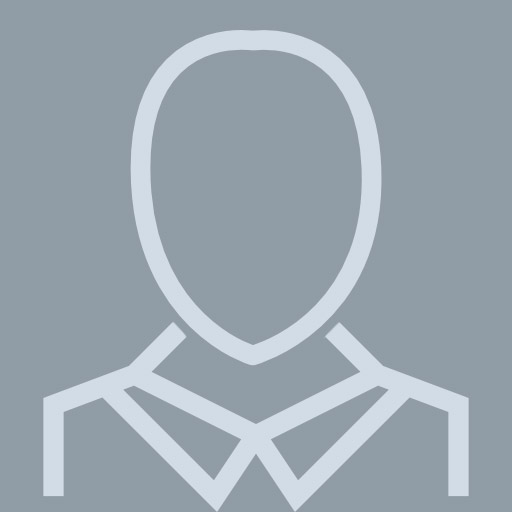
Guangyu Li
View pageSkills:
Microsoft Office
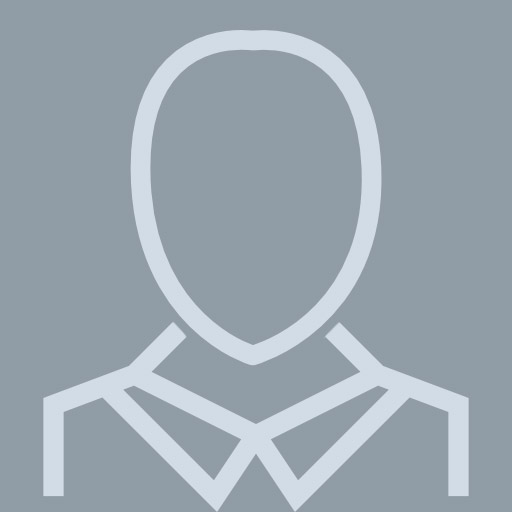
Laser And Optics Engineer
View pagePosition:
Laser and Optics Engineer at ESI
Location:
Portland, Oregon Area
Industry:
Electrical/Electronic Manufacturing
Work:
ESI since Dec 2005
Laser and Optics Engineer
Laser and Optics Engineer
Education:
University of Michigan 2000 - 2005
PhD, Electrical Engineering
PhD, Electrical Engineering
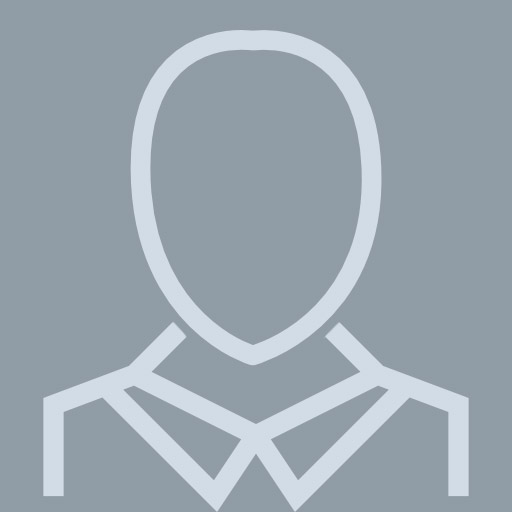