Resumes
Resumes
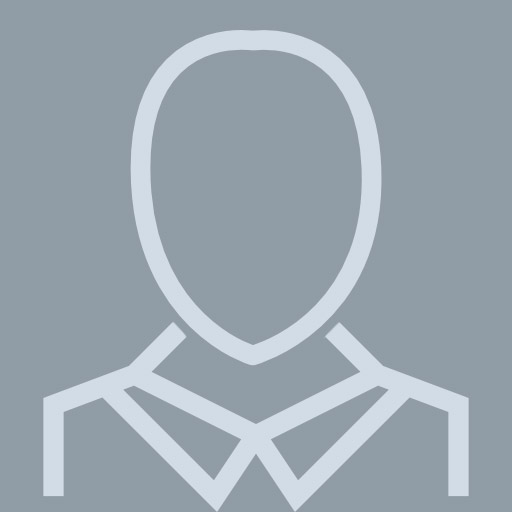
Engineering Specialist - Firmware And Controls
View pageLocation:
Peoria, IL
Industry:
Computer Software
Work:
Caterpillar Inc.
Engineering Specialist - Firmware and Controls
Caterpillar Inc. Oct 2016 - Jan 2018
Engineering Specialist - Electric Drive Controls
Caterpillar Inc. Oct 2010 - Sep 2016
Senior Software Engineer - Electric Drive Controls
Caterpillar Inc. Oct 2007 - Sep 2010
Software Engineer - Electric Drive Controls
Zempleo, Inc. Oct 2006 - Oct 2007
Engineer
Engineering Specialist - Firmware and Controls
Caterpillar Inc. Oct 2016 - Jan 2018
Engineering Specialist - Electric Drive Controls
Caterpillar Inc. Oct 2010 - Sep 2016
Senior Software Engineer - Electric Drive Controls
Caterpillar Inc. Oct 2007 - Sep 2010
Software Engineer - Electric Drive Controls
Zempleo, Inc. Oct 2006 - Oct 2007
Engineer
Education:
Bradley University 2005 - 2007
Masters, Electronics Engineering
Masters, Electronics Engineering
Skills:
Engineering
Product Development
Project Management
Six Sigma
Continuous Improvement
Matlab
Root Cause Analysis
Product Development
Project Management
Six Sigma
Continuous Improvement
Matlab
Root Cause Analysis
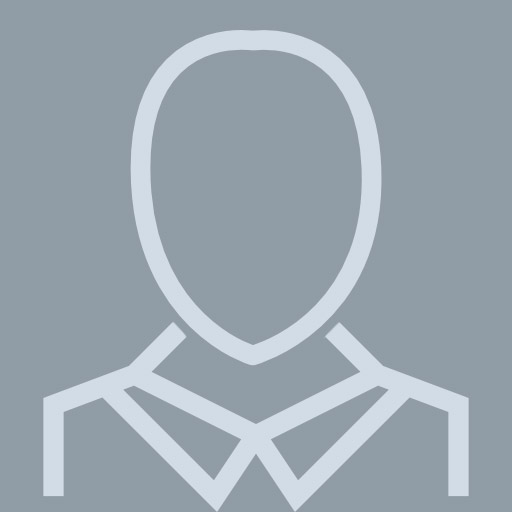
Engineering Specialist
View pageLocation:
Peoria, IL
Work:
Engineering Specialist